Back to where
you came fromRemember, a liter is 1 quart plus 3 tablespoons-
Utensil | Size in inches or quarts | Metric Volume | Size in Centimeters |
---|---|---|---|
Baking or Cake pan (square or rectangular) | 8 x 8 x 2 9 x 9 x 2 11 x7 x 1 1/2 12 x 8 x 2 13 x 9 x 2 15 x 10 x2 18 x 12 x 2 | 2 L 2.5 L 1.5 L 3 L 3.5 L 4.5 L 5.5 L | 20 x 20 x 5 22 x 22 x 5 27 x 18 x 3.5 30 x 20 x 5 33 x 23 x 5 39 x 25 x 5 44 x 30 x 5 |
Ring molds, bundt, angelfood or tube pans | 7 1/2 x 2 ring mold 7 1/2 x 3 bundt 9 1/4 x 2 ring mold 9 inch bundt 9 Inch angel 9 inch fancy tube 10 Inch bundt 10 Inch fancy tube 10 Inch angel | 1 L 6 cups 2 L 9 cups 9 cups 3 L 3 L 4 L 18 cups | 23 26 |
Brioche or turban pan | 9 1/2 x 3 1/4 | 2 L | 24 |
Loaf Pan | 7 1/2 x 3 1/2 8 x 4 x 3 9 x 5 x 3 | 1 L 1.5 L 2 L | 18 x 8 x 5 20 x 10 x 7 23 x 13 x 7 |
Flat pans | Biscuit 11 x 7 11 3/4 x 1 1/2 jelly roll 15 x 10 | 2 L 2.5 L 2.5 L | |
Round layer Cake pan | 8 x 1 1/2 9 x 1 1/2 | 1.2 L 1.5 L | 20 x 4 23 x 4 |
Round Springform pan | 8 x 3 9 x 3 | 3 L 4 L | 20 x 8 23 x 8 |
Pie Plate | 8 x 1 1/4 9 x 1 1/4 10 x 1 1/4 10 x 2 | 750 ml 1 L 1.25 L 1.6 L | 20 x 3 23 x 3 25 x 3 25 x 5 |
Baking dish or Casserole dish | 1 quart 1 1/2 quart 2 quart | 1 L 1.5 L 2 L |
Pan Sizes and Portions
3/8 cup
1/3 cup
1/4 cup
4 oz.
3 oz.
2.66 oz.
2 oz.
8
10
12
16
64
80
96
128
12'x20'x4'3 1/21/2 cup
3/8 cup
1/3 cup
1/4 cup
4 oz.
3 oz.
2.66 oz.
2 oz.
8
10
12
16
112
135
168
224
12'x20'x6'51/2 cup
3/8 cup
1/3 cup
1/4 cup4 oz.
3 oz.
2.66 oz.
2 oz.8
10
12
16160
200
240
320
289.1k Likes, 3,827 Comments - @snoopdogg on Instagram: '4 plus 1. Get y'all asses out the bubble. Laker gang 🔥💯🚨🚨🚨'. 1' deep: 300 square feet: 1' deep: 120 square feet: 2' deep: 150 square feet: 2' deep: 80 square feet: 3' deep: 100 square feet: 3' deep: 60 square feet: 4' deep: 75 square feet: 4' deep: 50 square feet: 5' deep: 50 square feet: 6' deep: 40 square feet: 6' deep: 25 square feet: 12' deep: 20 square feet: 12' deep.
Steam Table Pan Sizes and Capacities
Full-Size Pan (approximately 12×20)
Depth | Capacity in Quarts | 4-Ounce |
1 | 3½ quarts | 28 |
2 | 7 quarts | 56 |
3 | 11 quarts | 88 |
4 | 15 quarts | 120 |
6 | 22 quarts | 176 |
31½ quarts | 252 |
Half-Size Pan (approximately 10×12)
Depth | Capacity in Quarts (quarts) | 4-Ounce |
1 | 1½ quarts | 12 |
2 | 3½ quarts | 28 |
4 | 7 quarts | 56 |
6 | 10 quarts | 80 |
8 | 15 quarts | 120 |
Quarter-Size Pan (approximately 6x10)
Depth | Capacity in Quarts (quarts) | Paragon extfs for mac 11 3 30. 4-Ounce |
1 | 2 1/2 cups | 5 |
2 | 1¼ quarts | 10 |
4 | 3 quarts | 24 |
6 | 4¾ quarts | 38 |
Adapted from
Schmidt A. Chef's Book of Formulas, Yields, and Sizes. 3rd ed. Hoboken, NJ: Wiley and Sons; 2003.
Number and Approximate Size Servings Per Pan | ||||
---|---|---|---|---|
Pan | Approximate Pan Size | 24 25 | 50 | 100 |
Baking or Steamtable | 12'x20'x2 1/2' | 2'x3 3/4' | 2'x2' | .... |
Sheet or bun pan | 18'x26'x1' | 3 1/4' x 5' | 3 1/4' x 2 1/2' | 1 3/4' x 2 1/2' |
8 inch pie plate cut 4 servings | 8'x1 1/2' | 6 pies | 12 pies | 24 pies |
9 inch pie plate cut 6 servings | 9'x1 1/2' | 4 pies | 8 pies | 17 pies |
10 inch pie plate cut 8 servings | 10'x1 1/2' | 3 pies | 6 pies | 13 pies |
Cutting Portions from large pans or baking sheets, 18x26
For 25 servings cut 5x5
For 50 servings cut 5x10
For 100 servings cut 10x10
For 48 servings cut 3x8, then cut each rectangle diagonally.
1/8 teaspoon | .5 ml |
1/4 teaspoon | 1 ml |
1/2 teaspoon | 2 ml |
3/4 teaspoon | 4 ml |
1 teaspoon | 5 ml |
1 tablespoon | 15 ml |
2 tablespoons | 25 ml |
1/4 cup | 50 ml |
1/3 cup | 75 ml |
2/3 cup | 150 ml |
3/4 cup | 175 ml |
1 cup | 250 ml |
2 cups or 1 pint | 500 ml |
3 cups | 750 ml |
4 cups or 1 quart | 1 L |
Ounces | Tablespoons and cups | Milliliters |
---|---|---|
1 fluid ounce | 2 tablespoons | 30 ml |
4 fluid ounces | 1/2 cup | 125 ml |
8 fluid ounces | 1 cup | 250 ml |
12 fluid ounces | 1 1/2 cups | 375 ml |
16 ounces | 2 cups | 500 ml |
Ounces | Grams |
---|---|
1/2 ounce | 15 grams |
1 ounce | 30 grams |
3 ounces | 85 grams |
3.75 ounces | 100 grams |
4 ounces | 115 grams |
8 ounces | 225 grams |
12 ounces | 340 grams |
16 ounces or 1 pound | 450 grams |
Pan Swapping | ||
Pan Size | Equivalent Pans and Casseroles* | |
8' round pan | 9' pie pan | 11'x4-1/2' loaf pan |
9' round pan | 8' square pan OR 10' pie pan | 9'x5'x3' loaf pan |
9'x3' springform pan | 10'x3' bundt pan | |
9'x13' pan | two 9' round pans | or two 8' square pans |
15'x10' jelly roll pan | 9' square pan | two 8' round pans |
1 Quart casserole | 8 x 6 x 1½-inch baking dish | |
1-1/2-quart casserole | 9'x5'x3' loaf pan | 8 x 8 x 1½-inch baking dish |
2 quart casserole | 8' square pan | 9 x 9 x 1½-inch baking dish OR 12 x 7 1/2 x 2 inch |
2-1/2 quart casserole | 9' square pan | 10 x 10 x 1½-inch baking dish |
3 quart casserole | 9'x13' pan | |
4 quart casserole | 10'x14' pan | |
*adjust baking time if needed. Observe whether the new pan has the same DEPTH of ingredients as the original- if it makes a deeper layer, it will cook more slowly, shallower will cook more quickly. |
The new high-MERV filters extract an energy penalty.
MERV, the acronym for Minimum-Efficiency Reporting Value, is a measure of the efficiency with which filters remove particles of specific sizes. The test protocol for determining MERV ratings is described in ASHRAE Standard 52.2-2007, 'Method of Testing General Ventilation Air-Cleaning Devices for Removal Efficiency by Particle Size.' A MERV 8 filter can remove particles down to 3 microns in size at an efficiency of 70% or greater (1 micron is about 0.04 thousandths of an inch). Fiberglass and washable filters are typically 1–4 MERV, and can filter out particles of 10 microns and larger.
According to the Standard 52.2 application guidelines, particles in this size range include pollen, dust mites, mold spores, hair spray, powdered milk, and, of course, snuff. Higher MERV ratings (from 13 to 16) are needed to remove bacteria and smoke particles. At the top of the scale are HEPA filters with MERV ratings from 17 to 20, which can filter out particles smaller than 0.3 microns, including some viruses.
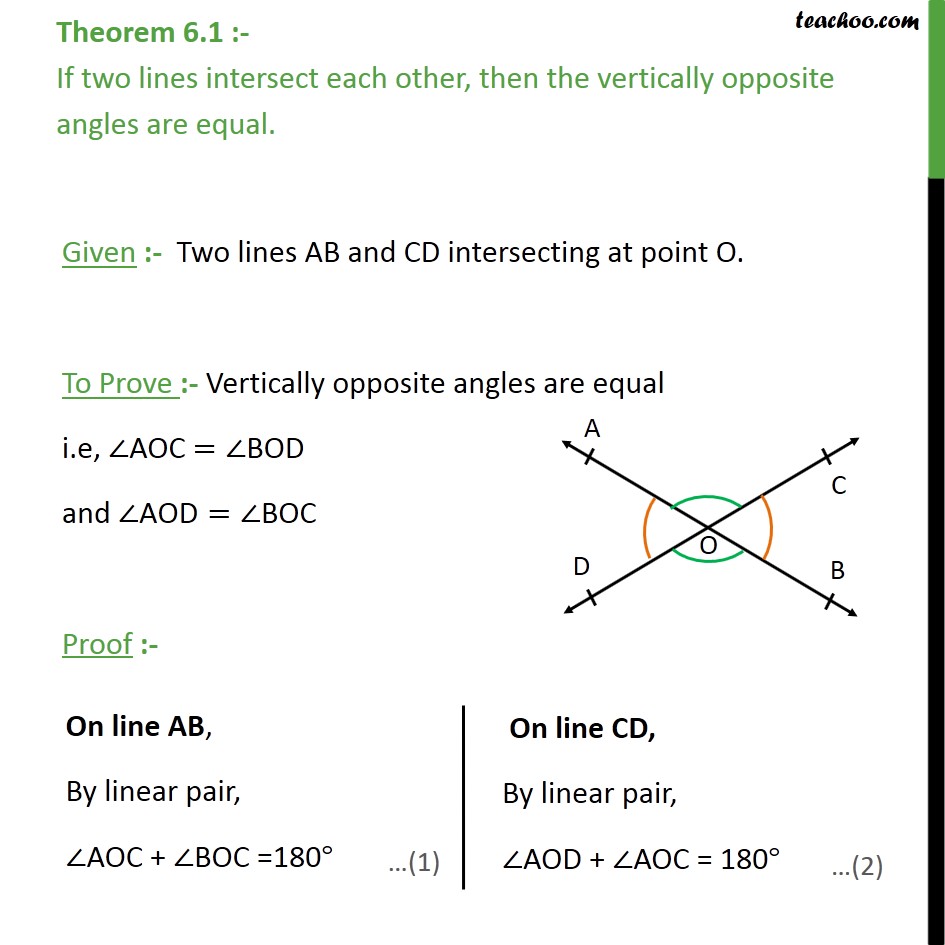
It stands to reason that the ability to filter smaller particles would come with the penalty of increased resistance to air flow. Could the shift to better filters mean that they could cause problems with inadequate air flow or greater fan energy use? Are all high-MERV filters equal, or do some have less pressure drop than others? How much better are 2-inch and 4-inch-thick pleated filters than 1-inch filters? Are larger ducts required to offset the added pressure drop of the filter? With a pat on the back from our Building America program sponsors, my colleagues and I at Davis Energy Group, in Davis, California, decided to run some tests to answer these questions.
Test Methods
We selected 13 filters for testing (see Table 1). The objective was to choose filters that homeowners would be likely to purchase to replace the filter provided by the builder, so we selected brands and models that are found in most big-box and chain retail stores, and that represent a variety of MERV ratings and thicknesses. We chose one fiberglass filter (ACE 30 Day) as a reference. Its rating was not listed, and we assumed that it was MERV 2. All except the Ace 30 Day and WEB Lifetime filters have pleated media. We purchased all but one of the filters (the Aeolus, a 2-inch MERV 13) from chain retail stores.
We decided to limit our tests to filters having outside dimensions of 16 inches x 25 inches. This is a commonly available size that allowed us to compare a wide range of products. Standard 52.2 specifies that filters be tested at 492 feet per minute (fpm) face velocity, which equates to 1,367 CFM for the 400 in² face area. Applying the 400 CFM-per-ton rule of thumb, this size would be appropriate for 3- to 3½-ton air conditioners.
Our testing evaluated filter pressure drop and blower motor energy over a range of air flow rates for each filter type. The test apparatus and measurement of standard air flow was based on ASHRAE Standard 41.2, 'Standard Methods for Laboratory Airflow Measurement,' (and used the equipment diagrammed in Figure 1). The apparatus included a calibrated nozzle box with integral pressure balancing fan, pressure sensors for measuring air flow and filter pressure drop, temperature and relative humidity sensors to normalize air flow to standard conditions, and power monitors for measuring blower energy. The filters were attached to a typical air handler that was coupled to the nozzle box. The blower wheel of the air handler was 12 inches in diameter by 10 inches wide.
We tested the filters using a standard ¾ hp PSC motor and a 1 hp GE ECM 2.3 variable-speed motor connected to the same blower. Most economy-priced furnaces use permanent split capacitor (PSC) motors. These respond to increasing flow restriction by moving less air with little change in power. The air flow reduction that occurs with PSC motors can affect the amount of power consumed by the compressor, and can also result in a decrease in cooling capacity, extended run times, and therefore greater energy use. Many higher-priced furnaces and heat pumps use electronically commutated motors (ECMs). These respond to increasing flow restriction by maintaining a fairly constant air flow rate, but at the expense of increased power and increased energy use. Testing with the ECM motor allowed us to 'dial in' the air flow rate, whereas the flow rate for the PSC motor was whatever it could deliver at its three different tap settings.
We wanted to determine the incremental impact of the filter on air flow and fan power beyond what the cooling coil and ductwork would contribute. California field studies have found that the median pressure drop for residential duct systems is 0.18 inches, and for cooling coils is 0.27 inches, resulting in a static pressure downstream from the filter of 0.45 inches. (The same field studies found that median pressure drops are 0.15 inches for both return ducts and filters, resulting in a total external static pressure of 0.75 inches (excluding the effects of the air handler/furnace internal system).
To simulate ductwork, we adjusted the pressure balance fan until the air flow and pressure drop fell on a typical flow versus pressure curve. The curve was developed by assuming that 1,400 CFM would produce 0.45 inches of static pressure at the discharge of the air handling unit. Thus, at different measured air flows, the virtual duct and coil pressure drop followed this curve, just as it would for a normal installed system.
Deeper 2 4 7 Equals Many
With the ECM motor installed, we evaluated filters at nominal air flows of 750, 1,000, 1,250, and 1,500 CFM. These air flows were set using a control that generates a pulse width modulation (PWM) signal that is proportional to the air flow the motor is programmed to deliver. The PSC motor was tested at each of its three tap settings. Second-order polynomial curve fits of each data set were used to interpolate filter pressure drop and power at the standard velocity of 492 fpm (air flow rate of 1,367 CFM).
Questions and Answers
We wanted to find out what penalties homeowners pay for switching to more efficient HVAC filters. Are the decreased air flow due to high-MERV filters and the added load on fans—meaning more energy used—worth the increase in indoor air quality that better filters bring? Here is what we found, in the form of questions and answers.
Do high-MERV filters reduce air flow?
Though there are considerable differences in how different filters affect air flow, there is a definite trend toward lower air flow with higher-MERV filters for systems using PSC motors (see Figure 2). Over the range of filters tested, there was no such correlation between air flow and filter MERV rating for the ECM motor, which can maintain constant air flow over a large range of external static pressure.
Do some high-MERV filters have higher pressure drop than others? Is pressure drop lower for thicker pleated filters?
There was a significant variation in pressure drop, particularly among the five MERV 8 filters tested, and not as close a correlation between pressure drop and MERV rating as we had expected to find (see Figure 3). The WEB Lifetime, a washable electrostatic filter, was the best high-MERV performer. Its MERV 8 rating is surprising, given the relatively open appearance of the media compared to the replaceable filters.
We also expected to see a lower pressure drop for the deeper 2-inch and 4-inch filters, because of the increased surface area and the reduced velocity of air passing through the media. Surprisingly, the 4-inch Filtrete 1550 (MERV 12) was only marginally better than the 1-inch Filtrete 1700 (also MERV 12) and the two other MERV 11 filters of the same brand (1000 and 1085). Of the two MERV 8 Flanders filters tested, the 2-inch Pre-pleat performed marginally better than the 1-inch NaturalAire. The other 2-inch entry, the MERV 13 Aeolus, had the second highest pressure drop of all filters tested. Because of their greater surface area, the thicker pleated filters may incur less pressure drop as they become loaded with particles, and may require less frequent replacement, but our testing was limited to clean filters only.
Most of the high-MERV filters tested substantially exceeded the median pressure drop of 0.18 inch obtained from the California field studies mentioned above. (According to Rick Chitwood, an energy consultant who has worked with the California Energy Commission, filters in these field studies were mostly inexpensive builder-installed fiberglass models.)
Do high-MERV filters increase fan energy use?
If the higher-MERV filter reduces air flow, as is the case with systems using PSC motors, it has only a very slight impact on fan energy use. But if ECM motors are used, the impact can be significant (see Figure 4). Figure 5 illustrates the difference in energy use of PSC and ECM motors relative to filter pressure drop. Although higher MERV filters will increase the fan energy use of ECM-equipped systems, ECM motor energy use is far less than that of PSC motors.
Will the reduced air flow rates of high-MERV filters in PSC systems affect compressor energy use?
Air conditioner and heat pump rated performance is a function of air flow over the indoor coil. Lower air flows can decrease capacity and consequently the energy efficiency ratio or heating seasonal performance factor of the system. We looked at representative manufacturers' performance curves and found that, over the less than 200 CFM reduction in air flow observed between the MERV 2 and MERV 13 filters (see Figure 2), the effect of the filters on compressor power is very slight. However, the pressure drop of filters can more than triple when they are fully loaded with dust particles, so loaded filters probably will affect system performance. The deeper pleated filters allow the dirt to be spread over a larger surface area, reducing pressure drop and making it possible to change the filter less often without significantly affecting system performance.
What can be done to mitigate the added pressure drop of high-MERV filters?
Friction contributed by coils, ductwork, and filters is additive, so reducing the friction of one component will offset the added friction of another. When completing ACCA Manual D duct sizing, a realistic filter pressure drop should be used. If using a MERV 8 or higher filter, a pressure drop value of at least 0.5 inches should be entered for the filter. In one Manual D example we ran, we found that increasing the filter pressure drop assumption from 0.2 inch to 0.5 inch did increase the required size of some of the ducts.
Oversizing the filter to decrease the face velocity will substantially reduce pressure drop, provided the equipment can accommodate larger filters. Figure 6 shows the pressure drop versus face velocity curve measured for the Filtrete 600. At the standard 492 FPM face velocity, the static pressure is about 0.32 inch WC. Increasing the filter size by 25% reduces the static pressure to 0.20 inch, and doubling the filter size reduces it to about 0.07 inch.
How do measured fan power values compare to industry standards and field data?
At the 1,367 CFM standard air flow used in these tests, PSC motor power ranged from 0.502 to 0.523 watts/CFM (W/CFM), and ECM power ranged from 0.347 to 0.390 W/CFM. In calculating air conditioner SEER ratings, assume 0.365 W/CFM fan energy (unless data are supplied by the manufacturer). California Title 24 standards apply a more realistic 0.58 W/CFM prescriptive fan energy value. Median values obtained from Lawrence Berkeley National Laboratory tests of 141 furnaces were 0.44 W/CFM, and test data from new California homes yielded a median value of 0.52 W/CFM.
Irrespective of the measured impacts of high-MERV filters on system energy use, SEER ratings appear to significantly underestimate the contribution of fan power. California field test results and Title 24 default W/CFM values are reasonably consistent with our laboratory tests of the PSC fan with clean filters—all are considerably higher than the 0.365 W/CFM default value. As high-MERV filters become more prevalent, DOE should give consideration to establishing a default value that is at least consistent with clean MERV 8 filters. More research is needed to the impact of dirt-laden high-MERV filters on energy use and air flow.
Lessons Learned
It takes immense patience to measure the air flow of ECM-powered fan systems accurately. Particularly if a pressure balance fan is used to adjust the static pressure seen by the blower, the motor reacts dynamically to the changing pressure and interacts with the pressure balance fan, making it very difficult to zero in on a particular set of pressure conditions. ECM motors also have harmonics that might confuse some power monitors. We found fairly good agreement between a precision (Dent) power monitor and an inexpensive (Kill-A-Watt) meter. Interestingly, using multiple wraps around the current transformer to improve measurement resolution produced erroneously low power measurements.
Fulfilling Filter Potential
System designers and other HVAC professionals should know the effects of high-MERV filters on pressure drop and system performance. However, if no accommodations are made for the greater pressure drop of high-MERV filters, air flow and energy penalties are not likely to be severe—at least, not until the filter is loaded with dirt. Care must be taken to reduce register and grille, duct and plenum, and filter pressure drops to ensure a sustainably efficient system. Making filters accessible for easy replacement, and providing controls that tell homeowners when replacement is due, will help to eliminate problems such as clogging and filter collapse that are more likely to occur with the more efficient filters.
As we have shown, there is a wide variation in pressure drop performance, particularly among the MERV 8 filters, and inadequate product labeling makes it difficult to make informed choices. Some product labels do not list MERV rating, and none lists standard pressure drop.
Although ASHRAE Standard 52.2 does not address the energy implications of filtration, there is growing interest in this subject on the part of its members. A recent ASHRAE paper presents two methods for rating the energy performance of filters, and we may expect an expansion of Standard 52.2, or the development of other standards, that will incorporate filter energy ratings as emphasis on energy efficiency grows.
Incidental to the filter evaluations, the data reveal the significant energy savings potential of properly designed systems with variable-speed ECM motors. However, these motors will degrade system performance if there is excessive pressure loss in filters, coils, and ductwork. Some furnaces are beginning to incorporate a newer non-variable-speed brushless permanent magnet motor, the GE/Regal Beloit ECM X13. This motor should use about the same amount of power as the ECM 2.3 version tested, but since it does not regulate air flow, its power use will be relatively unaffected by filter pressure drop associated with a high-MERV rating or dirt accumulation.
Deeper 2 4 7 Equals The Square Root
David Springeris President of the Davis Energy Group (DEG), a Davis, California engineering consulting firm, leads DEG's Building America activities, and is an active member of ASHRAE. While he is a strong radiant heating advocate, he appreciates the importance of filtering ventilation air.
For more information:
For more on the California field studies of duct pressure drop, see www.energy.ca.gov/title24/2008standards/prerulemaking/documents/2007-06-13-15_workshop/presentations/Wilcox070613c1.pdf
Sun, C., and D. Woodman. 'Delivering Sustainability Promise to HVAC Filtration,' pt. 1: 'Classification of Energy Efficiency for Air Filters.' ASHRAE Transactions 115, pt. 2 (2009).
- FIRST PAGE
- PREVIOUS PAGE
- NEXT
- LAST